What is Raku Pottery?
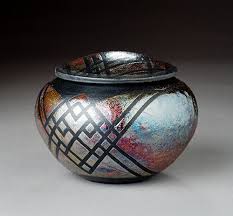
Raku is a pottery technique that originated in Japan in the 16th century. The technique involves a specific rapid firing process at a relatively low temperature but the whole process can be much more complex.
The technique has developed and there is now the traditional Raku and a western version of Raku. The results of this type of process are very unique from other firing techniques, and some fantastic metallic finishes, crazing and other decorative effects can be achieved.
The process in brief
In raku, the pottery pieces are loaded into a cold kiln (for multiple batches pieces are often preheated and loaded into a hot kiln). The kiln is heated rapidly with the ware reaching temperature in as short a cycle as 15-20 minutes.This contrasts with traditional firing cycles of 10 hours or more!
Glaze maturity is judged by the trained eye without the use of cones or measuring devices. Often this is when the glaze has begun to melt.
When the firing is considered to be complete the ware is immediately removed from the kiln while still red hot using tongs or another lifting device.This is the stage in the process where traditional and western raku differ in technique and treatment.
In the western version the ware is treated to a post firing reduction. To achieve this the hot ware is put into a container, usually a garbage can, with combustible material such as paper, sawdust, or leaves and allowed to smoke for a predetermined length of time (usually about 20 mins). The carbonaceous atmosphere (black sooty smoke) reacts and affects the glazes and clay and imparts unique effects and surfaces to the wares. Some of these effects are metallic and crackled glazes surfaces and black unglazed clay.
When the ware has cooled, it is washed with an abrasive cleaner to remove all residues of soot and ash. In this way it is possible to produce a unique piece of art pottery. Unfortunately because of this rapid process the ware is relatively fragile and the decoration not food safe. Pottery made in this way must only be used for decorative purposes.
The Process in detail
The Clay body
Raku bodies are designed so that they allow rapid heating and cooling without cracking. Most raku bodies (but not all) use a recipe that is high in grog (coarse material). A range of Raku bodies are available from suppliers to match your making and firing process.
A typical body recipe might include by parts weight:-
Clay 65-75%
Grog 25-35%
Talc 0-15%
The type and amounts of each component will depend on many factors. These include the clay making process, the fired body colour and texture required and the firing temperatures to be used.
One of the important questions you need to answer "will the glaze and body combination I intend to use give me the glaze finish I require?". For example many glazes used on Raku will readily craze if the correct glaze/body combination is not used. For some this might be an appealing effect. For other Raku makers it may not. So choose your clay body wisely.
The clay body for raku is typically bisque fired to cone 04 (1060C) prior to glazing. This gives it sufficient strength for handling during the glaze firing process, as well as some porosity to aid glaze application.
Most clay suppliers will help you choose an appropriate clay body. Biscuit firing of the clay piece is essential if the pottery is to avoid breakage on firing.
The Glaze
Next you can apply slip, apply glaze, or just leave the pot bare. Any glaze that will melt successfully during the raku fire could be used. The most important factor in identifying potential raku glazes is the temperature at which they mature, how you plan on using them, and what kind of effects you are looking for. Low fire glazes generally give the best results. Most raku is fired in the range of cone 010-06. (900-1000C) Note the surfaces of the pot that are not covered with glaze will however turn black from carbon from the post-firing reduction process.
For more info on Raku glazes see my separate article on
Raku glazes.
Raku (glaze) firing
 |
Northern Kilns Raku kiln |
The pottery is placed in the kiln and rapidly heated to the point at which the glaze melts. Although a pyrometer is sometimes used to monitor how fast the temperature is rising, Raku artists usually watch the glaze to see when it is ready to be removed from the kiln. Depending on the glazes and technique used, this might be when it gets shiny, or when it bubbles and/or looks like orange peel. Transfer of the ware from kiln to the reduction chamber is important. Speedier transfers can give metallic lustres whilst slower transfer can give brighter colours.
Types of Raku kiln
For firing of multiple loads the temperature of the kiln must also be readily controllable. An electric kiln is perfectly suitable for raku although there are some special considerations that require careful attention. Cut off switches must be used to avoid any contact with live electrical current when the electric kiln is opened.
Many types of gas and electric kilns can be used for raku. Kilns need to be located outdoors or in close proximity to the outdoors or have lots of ventilation. Access to the pots inside the kiln is critical so they can be easily removed. Raku kilns are therefore designed to provide this easy access to red hot pots.
More information on Raku firing can be found the
Potters Friend website
The Reduction Process

The reduction chamber (garbage can) is prepared by adding the combustibles. There are many things that can be used, but newspaper, sawdust, or wood chips work well and is abundant. After switching off, the kiln is opened and hot piece removed from the kiln with tongs or a lifting device. Immediately it is placed in the reduction chamber (garbage can) where the heat sets the combustibles alight. The lid of the can is replaced and the chamber left for about 20 minutes.
After the pot has completely cooled, it is possible to use Ajax cleaner or similar to clean carbon off the glaze and "shine up" the piece. Reduction is a firing term that refers to a lack of oxygen in the combustion process. By sealing the can with the lid the can is deprived of oxygen. This lack of oxygen causes incomplete combustion of the paper or sawdust to take place and creates the metallic finish on the glaze.
Safety
The raku process is a dangerous process as you will be exposed to high heat, flames and smoke. Always wear fire protective clothing, fireproof gloves and protective eyewear. Do not open or insert tongs into an electric kiln without shutting off. The reduction process (container with combustibles) should take place outside of building due to flames and smoke.
Do not apply spray glazes without a NIOSH approved respirator and other personal protective equipment.
Although many glazes are Non Toxic and Non Hazardous when used according to manufacturer’s directions, this is not always the case. It is important to check! Raku glazed items are suitable only as decorative ware and are not recommended for contact with foodstuffs.