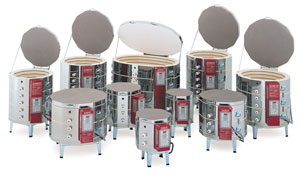
The firing of pottery goes back over 3000 years. In those days wood fires were the source of energy. However today so many other forms of energy are available including wood, coal, gas, electric, oil, microwave, wind, solar to name just a few.
For the small pottery craft studio or hobbyist however the most common means of firing pottery are by the use of gas or electric kilns. Generally electric firing is a clean means of firing whilst gas is thought to be more energy efficient. Let us consider the basics of each:
How does electric firing work?
The principle of electric firing is relatively simple. Imagine a box or cylinder kiln fitted with heating elements like your domestic oven. However, instead of heating to 300C it is capable of heating to 1300C.
Operation of the kiln starts when electricity is applied to the elements ( resistive load ) causing them to heat rapidly. The heat is transmitted to the pottery mainly by radiation. Special insulating bricks, called refractories, line the floor,walls and roof of the chamber to prevent the heat generated from escaping. An electronic box, called a temperature controller,linked to a thermocouple (special wire) inside the kiln, measures the temperature constantly in the chamber of the kiln and then controls how much electricity is supplied to the elements. This in turn controls the rate of increase or decrease in temperature within the kiln.
How does gas firing work?
The principle of gas firing is also relatively simple.. Imagine this time that the box is kiln fitted with a burner or burners, a little like your domestic gas oven. However, instead of heating to 300C it is capable of heating to 1300C and because of the large amount of gas used the kiln needs a chimney or flue.
Operation of the kiln starts when the gas is turned on and burner lit. The heat is transmitted to the pottery mainly by convection and radiation causing it to heat also. Special insulating bricks, called refractories, line the floor,walls and roof of the chamber to prevent the heat generated from escaping. A vent in the roof or rear of the kiln leading to a chimney allows combustion gases to be removed from the kiln. An electronic box, called a temperature controller,linked to a thermocouple (special wire) inside the kiln, measures the temperature constantly in the chamber of the kiln and then controls how much gas is supplied to the burner. This in turn controls the rate of increase or decrease in temperature within the kiln.
How do I fire the kiln properly?
For both electric and gas firing the two critical factors which affect the success of your firing are peak temperature and uniformity of temperature within the kiln. Peak temperature can easily be measured using the thermocouple fixed inside the kiln. Uniformity could also be measured using a series of such thermocouples located in different sections of the kiln. However this would be an expensive option for smaller kilns.The use of Bullers Rings or pyrometric cones to confirm the consistency and uniformity of firing at different locations within the kiln is more cost effective.These ceramic cones or rings can be placed next to your ware and will experience exactly the same amount of heat as your item. By measuring the values of the rings or cones after each firing you can be assured the firing is consistent from one firing to the next.
But what is the peak temperature?
The peak temperature on firing biscuit or glaze is the maximum temperature reached on firing. This value depends on the type and composition of the clay body and glaze used. As there are literally thousands of body and glaze compositions,suppliers of body and glaze products therefore recommend a peak temperature or ring or cone value equivalent suitable for optimum firing their products. It is advisable to follow their recommendation.
But what if the temperature isn't consistent?
Quite often there is a spread of temperature within the kiln. It is quite common to have a 20 C spread in temperature between the bottom and top of even small kilns. The reason for this is dependent on a number of factors. Rate of firing, kiln design and condition (age and condition of brickwork),element condition and age (for electric kilns) gas/air ratios and flame (for gas kilns) and ventilation aspects of the kiln are all key factors.
For uniform firing of kilns a slower temperature rise to peak temperature and a soak at peak temperature will reduce variation of temperature within the kiln. Indications of non uniform firing of glazed pottery are variation of gloss, colour and or bubble between similar fired pieces.
Summary
Peak temperature and uniformity of temperature are the key factors determining the success of your pottery firing. Peak temperature is measured using a thermocouple connected to the digital display of a temperature controller. Uniformity is measured using Bullers rings or Cones placed in the kiln next to the ware. The heating rate has an affect on both and should be relatively slow for best results. A cycle of more than 12 hours cold to cold is quite common. However you should be guided by the body or glaze supplier as they know the optimum cycles for their products.
More information on firing of pottery and ceramics,including Bullers rings and Orton cones, can be found at my website http://www.pottersfriend.co.uk Go now to sign up for my free newsletter.